Seal ring
Luminar marine's ABR-2 New Seal Ring Material
Polymer materials of our rubber seal ring
Generally, filler particles are added to polymer materials to get highly reinforced properties imparted to final product. However, processing of such composite leads to process difficulties due to chemical nature of the fillers and polymers. The fillers used widely have hydrophilic surfaces and their interaction with hydrophobic polymers leads to increase in processing viscosity and aggregation of the filler particles. Such composite leads to poor reinforcement having degraded properties of polymer composite.
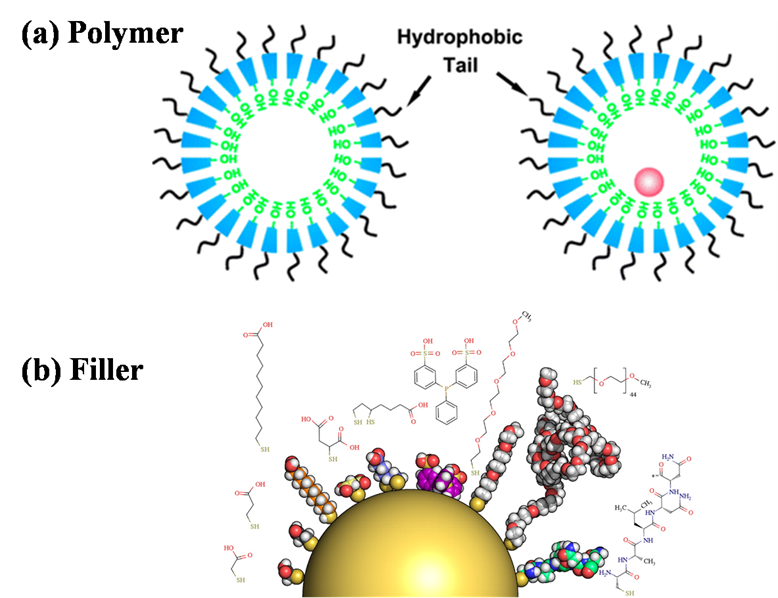
Schematic of polymer hydrophobic and filler hydrophilic surfaces
To overcome the problem associated with processing and improving the reinforcement of polymer composite, we have developed a novel technology for the first time by years of research and development. Our selection of special filler material imparts hardness and abrasion resistance to composite structure. At the same time, surface treatment improves the processing ability with respect to low viscosity, less aggregation and improved reinforcement leading to higher life time of the polymer composite.
To overcome the problem associated with processing and improving the reinforcement of polymer composite, we have developed a novel technology for the first time by years of research and development. Our selection of special filler material imparts hardness and abrasion resistance to composite structure. At the same time, surface treatment improves the processing ability with respect to low viscosity, less aggregation and improved reinforcement leading to higher life time of the polymer composite.
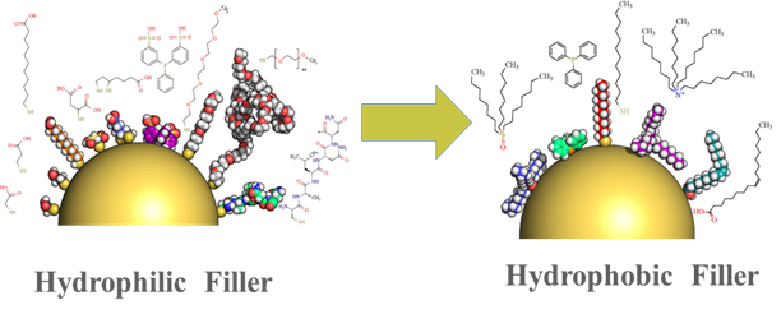
Schematic of surface treatment of new filler material
The surface treatment of hydrophobic new filler material leads to hydrophobic surfaces which can interact with hydrophobic polymer matrix leading to low viscosity, no aggregation of individual particles, high mechanical strength, improved abrasion resistance and longer life time.
The surface treatment of hydrophobic new filler material leads to hydrophobic surfaces which can interact with hydrophobic polymer matrix leading to low viscosity, no aggregation of individual particles, high mechanical strength, improved abrasion resistance and longer life time.
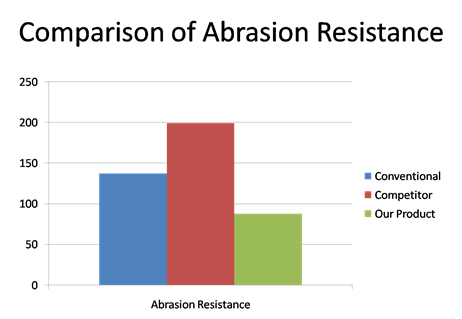
Our specially developed composition resulted in superior compatibility with bio-degradable lubricating oil and the volume shrinkage is at the lowest level using our seal. Our new seal ring can be used specifically for bio-degradable lubricating oil owing to its superior mechanical and chemical resistance. Using our specialized chemical processing of new material, the activation energy is lowered so that stronger bonds are favorable under processing conditions. Such highly improved chemistry leads to very high endurance and imparts longer life almost two to three times that of conventional seal.
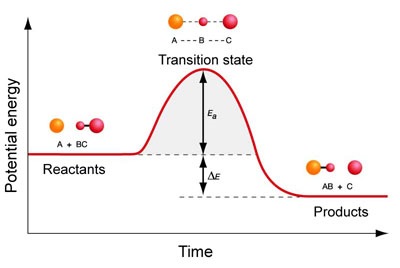
Graph of Activation Energy
In particular, our new polymer material leads to the low volume shrinkage for the polymer composite which is critical for sealing application. It can be seen that the volume shrinkage is lowered to minimum against pristine polymer imparting longer life to the seal.
In particular, our new polymer material leads to the low volume shrinkage for the polymer composite which is critical for sealing application. It can be seen that the volume shrinkage is lowered to minimum against pristine polymer imparting longer life to the seal.
Properties of our seal ring product
We have tested our product in-house as well as by third party certification companies. The following are the properties exhibited by the seal made using the novel composition.
TEST ITEM | UNIT | RESULTS | TEST METHOD | |
---|---|---|---|---|
Hardness | – | 91 | ASTM D 2240:05(2010) | |
Tensile strength | MPa | 23.6 | ASTM D 412:06a(2013) | |
100% Modulus | MPa | 13.9 | ASTM D 412:06a(2013) | |
Elongation | % | 148 | ASTM D 2240:05(2010) | |
Compression set | % | 9.7 | ASTM D 395:03(2008) (200±1)℃, 22h, 25% compression |
|
Abrasion·DIN | mm³loss | 78.4 | ISO 4649:2010 | |
Oil Resistance | Hardness Change | – | 0 | ASTM d 471:12a #3 oil (65±1)℃, 168h |
Volume Change | % | +0.5 |
Test results
Comparison with conventional products
We have tested our products extensively and compared with the product by our competitors under ideal analysis conditions. The properties are listed as follows.
Parameter | Conventional product | Competitor’s product | Our product |
---|---|---|---|
Hardness | A90 | A89 | A91 |
Abrasion Resistance | 137.4 | 199.1 | 78.4 |
Elastic Modulus | Failed | NA | 14.9 |
Oil Resistance Volume Change |
+0.4 | -0.3 | +0.4 |
It can be seen that our product not only showed improved hardness, abrasion resistance and low volume shrinkage, but also very high endurance that resulted in longer life time
Luminar marine's ABR-2 seal ring
All of our seal ring products are compatible with Environmentally Acceptable Lubricants (EALs)